Dyeing of Cotton Fabric with Reactive Dye
What is Reactive Dye in Textile?
Reactive Dyes have long been known to give a high degree of fixation because with two potential vinyl sulphone reactive groups there is an increased probability of reaction with the fiber. Many of the new reactive dyes are bi-functional with identical or different reactive groups in the dye molecule. Adding more reactive groups to a given chromophore increases the molecular weight but decreases the color per unit weight of dye since the reactive groups are not part of the chromophoric system. This problem can be partly overcome, for example by linking together two DCT dyes with a suitable diamine to give a dye with two MCT groups, as in the Procion H-E dyes. This increase in molecular size usually results, in an increase in substantivity. That is the value for exhaust dyeing with high liquor ratios but which can impede the washing-off of unfixed dye after dyeing Bifunctional dyes with two reactive groups of different reactivity towards the cotton, which have different optimal fixation conditions, give a more uniform degree of fixation over a wide range of dyeing temperatures and fixation PH than dye containing two identical groups. This type of reactive dye gives quite high fixation yields and thus less color in the dyehouse effluent. Other important types of bifunctional reactive dyes include the MFT-VS type and the MCT-VS type used in the suffix supra dyes. The kayacelon react range for dyes are also bifunctional reactive dyes, having two NT reactive groups in each dye molecule
History of Reactive Dyes:
On the occasion of a thousand-year celebration of synthetic dye manufacturing, two chemists of ICI company (UK) named Steffen and Ratte tried to manufacture new dyestuff. Thus they succeeded in inventing a new dye in 1956 which was named Reactive dye. This was manufactured for dyeing cellulosic fiber.
The first three reactive dyes are procion yellow R, procion brilliant Red 2B, and procion blue 3G. For this effort, they were awarded the gold medal of the Society of Dyes and Colorists for the year 1960. These dyes came to our country in the mid-'60s and became very popular in the '80s.
The dyeing of cotton with direct dyes has poor washing fastness. Because it has a weak bond with the dye molecules in the cellulose polymer chains. So direct dyes can easily come out from the fabric molecules. For best washing fastness insoluble pigment is attaching it with the cotton fibers. This type of dyeing process of vat, sulfur, and azoic dyes is much more difficult than direct dyeing. The idea of forming a dye molecule covalent bond with the reactive group in a fiber originated in the early 1900s. Various chemicals were found that reacted with the hydroxyl group of cellulose and eventually, they converted into colored cellulosic derivatives. Cellulose was a relatively unreactive polymer. As a result, several dyes are known to be capable of forming bonds with wool. Initially, cotton was not considered a fiber-reactive dye, although it has good washing fastness. In 1955, developed a procedure for dyeing cotton with fiber-reactive dyes. They established that dyeing cotton with these dyes under mild alkaline conditions resulted in reactive chlorine atoms. The role of alkali is to cause acidic dissociation of some of the hydroxy groups of cellulose and it is the cellulose ion that reacts with the dye
The dyeing has a very good washing fastness. The only possibility of bleeding dye from the cotton is after the hydrolysis of the covalent bond between the dye and the cellulose. Within five years of this development, all the major dyestuffs manufacturers were marketing reactive dyes of cotton and wool. Because of their good washing fastness, bright shades, versatile batch, and continuous dyeing method, reactive dyes have become one of the major classes of dye.
Structure of reactive dyes for cotton:
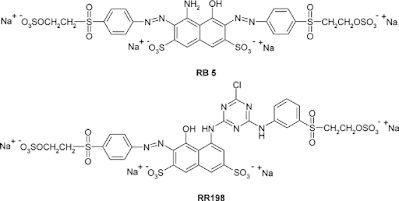
The structural key features of reactive dyes are the chromophore system, the sulphonate group for water solubility, the reactive group, and the bridging group that attaches the reactive group either directly to the chromophore group or to some other part of the dye molecule. Each of these structural features can influence the dyeing and fastness properties in the dyeing textile manufacturing process. Most commercial ranges of reactive dyes have a complete gamut of colors, many of which are particularly bright. Reactive dyes often have simple structures that can be synthesized with a minimum of colored isomers and byproducts that tend to dull the shade of the more complex palazzo-direct dyes. Some colors are difficult to obtain with simple chromophores. Dark blue and navy reactive dyes are often rather dull copper complexes of azo dyes and the production of bright green reactive dyes remains a problem.
A whole range of possible fiber reactive groups has been examined and evaluated by the dyestuff manufacturers. The final choices for commercial dyes are limited by several constraints. The reactive group must exhibit adequate reactivity towards water that can deactivate it by hydrolysis. The hydrolysis of the dye's reactive group is similar to its reaction with cellulose but involves a hydroxyl ion in water rather than a cellulose ion in the fiber. In addition, the dye fiber bond, once formed should have adequate stability to withstand repeated washing. Other factors involved are the ease of manufacture, the dye stability during storage, and the cost of the final reactive dye
HO-+ Dye -Cl = Dye-OH + Cl-
Types of Reactive Dyes:
- Those reacting with cellulose by nucleophilic substitution of a chlorine, fluorine, methyl sulphone, or nicotine leaving group activated by an adjacent nitrogen atom in a heterocyclic ring.
- Those reacting with nucleophilic addition to a carbon-carbon double bond, usually activated by an adjacent electron attacking sulphone group. This type of vinyl sulphone group is usually generated in the dyebath by the elimination of sulfate ion from a 2- sulphatoethylsulphone precursor group with alkali.
Although many of the early reactive dyes had only one reactive group in the dyestuff molecule, many of the newer reactive dyes function with two or more identical or different reactive groups. Some typical fiber reactive groups and the commonly used abbreviations for these groups. Dyes with nicotinyltriazine reactive groups react with cotton on heating under neutral conditions.
Basic Principle of Reactive Dyeing Process of Cotton Fabric:
The relatively simple procedure for batch dyeing of cotton materials with reactive dyes is still used for all types of reactive dyes irrespective of their particular reactive group. Dyeing is commenced in a neutral solution, often in the presence of salt to promote exhaustion of the dye onto the cotton. During this period, the dye does not react with the fiber, and migration from fiber to fiber is possible. Then, an appropriate alkali is added to the dye bath to increase its PH. This initiates the desired dye fiber reaction. The hydroxyl group in cellulose4 is weakly acidic and absorption of hydroxide ions causes some dissociation, forming cellulosate ions. It is these that react with the dye by
nucleophilic addition or substitution. In general, the lower the reactivity of the reactive group towards the alkaline cellulose, the higher the final dyeing temperature and the higher the PH of the dye bath.
Unfortunately, under alkaline conditions, hydroxide ions also react with the reactive group of the dye. This produces the hydrolyzed dye, which is incapable of reacting with the fiber. Hydrolysis of the dye is slower than the reaction with the alkaline cotton but it is significant and reduces the efficiency of the fixation process. After dyeing, an unreacted and hydrolyzed dye present in the cotton must be removed through washing. This ensures that no color will bleed from the cotton on subsequent washing during use. The higher the substantivity of the reactive dye for the cotton, the more difficult to wash out the unfixed dye from the material. Many of the first reactive dyes had quite simple molecular structures and low substantivity for cotton so the removal of hydrolyzed dye from the material by washing was relatively easy. This is not necessarily true for reactive dyes of more complicated molecular structures.
Dye Reactivity, Storage, and Application of Reactive Dyes:
The reactive groups of various types of dye have different chemical structures and show a wide range of reactivities. They were originally divided into cold and hot dyeing types but many current ranges would be better called warm dyeing. The most reactive dyes such as DCT reactive dyes are applied at lower temperatures (20-40)C and only require a weak alkali such as NaHCO3 or Na2CO3 for fixation. The less reactive dyes such as MCT dyes, need higher temperatures(80-90) C and stronger alkali such as Na2CO3 Plus NaOH. Many dyestuff manufacturers now market several ranges of reactive dyes for cotton, each with its own particular recommended dyeing procedure. Below are some examples based on the type of reactive grouping:
- Reactive Group(DCT)- Commercial name: (Procion MX) BASF - Reactivity(High) - Temp(25-40)C
- Reactive Group(MCT)- Commercial name: (Procion H, Basilen)BASF & Cibacron (Ciba) - Reactivity- (Low) Temp(80-85)C
- Reactive Group(MFT)- Commercial name: (Cibacron F) Ciba - Reactivity (Moderate)- Temp(40-60)C
- Reactive Group ( DCQ)- Commercial name: (Levafiz E) Dystar- Reactivity (Low) - Temp(50-70)C
- Reactive Group (DFCP)- Commercial name: (Drimarene K) Clarient, (Levafix EA) Dystar- Reactivity (moderate to high) - Temp(30-40)C
- Reactive Group (VS)- Commercial name: (Remazol) Dystar -Reactivity- (Moderate)- Temp(40-60)C
- Reactive Group (TCP)- Commercial name: (Drimarene X) Clarient- Reactivity- (Low) - Temp ( 80-95)C
- Reactive Group (NT)- Commercial name: (Kayacelon React) Nippon Kayaku- Reactivity- (Moderate to High) - Temp (100-130)C
The above reactive groups react under neutral conditions. Because most reactive dyes are prone to hydrolysis, their handling and use require care. Most are readily water soluble and the dye solution is prepared in the usual way by pasting it with water and then adding more water. The temperature of the water used depends upon the ease of solution and the reactivity of the dye. Hot water is not recommended for dissolving dyes of high reactivity, because of the risk of the hydrolysis of the reactive group, but it is suitable for the less reactive dyes. Once the dye solution has been prepared, it cannot be stored for later without some risk of hydrolysis of the reactive group. This decreases its fixation ability and it is a particular problem with most of the reactive dye. Dyes containing 2- sulphatoethylsulphone group, however, can be dissolved in neutral water in the boil without risk of hydrolysis. Formation of the reactive vinyl sulphone group requires the addition of an alkali.
Reactive dyes for printing are usually dyes of low reactivity so that the print paste can be stored for some time at room temperature without deterioration from hydrolysis of the reactive group. Reactive dyes of low reactivity and relatively high substantivity are valuable for dyeing using long liquor ratios, using a winch machine. Exhaust dyeing with low reactivity dyes at the higher temperature required for fixation allows better penetration of the dyes into the cotton fibers. For continuous dyeing of reactive dyes stabilized liquid forms are available. Although these contain special PH buffers and stabilizers to minimize the hydrolysis reaction, they only have a limited shelf life Many commercial reactive dyes are dusty powders but all physical forms must be handled with care. These dyes react with the amino groups in proteins in the skin and on mucous surfaces. Inhalation of the dust is dangerous and a dust mask is obligatory during handling. Reactive dye powders and grains are sometimes hygroscopic and drums must be carefully resealed. Most reactive dyes have a limited storage period, after which some deterioration can be expected. Standardization and comparison of reactive dye powders or liquids cannot be done by the usual spectrophotometric procedure involving absorbance measurements of standard solutions. Both the reactive dyes and their hydrolyzed forms are equally colored. but only the former is capable of reacting with the cellulose during dyeing. Chromatographic techniques usually allow separation and quantitative measurements of the relative amount of a reactive dye and its hydrolysis product in a given dye
Reactive Dye Properties
- Reactive dye is anionic in nature
- Reactive dye is a water-soluble dye
- They have better wash and light properties
- They have better substantivity
- They form strong covalent bonds with the cellulosic fiber
- Alkaline conditions are required for dyeing
- Electrolyte is required for dye exhaustion in the fiber
- A wide range of colors can produce
- Comparatively cheap in price
Reactive Dyes Uses:
- Reactive dyes are used where bright dyeing with high light and wash fastness is required
- Cold dyeing is extensively used in basic work
- Although some reactive dyestuff have been specially modified to dye wool fiber, their main uses in dyeing cotton linen and viscose rayon
Fastness Properties of Reactive Dyes on Cellulosic FibersIn general, reactive dyes on cellulosic fibers give good dyeing with very good washing fastness and other wet processes. Apparent inferior fastness to washing is usually because of incomplete removal of unreacted and hydrolyzed dye from the material by washing after dyeing. The presence of unfixed dye can easily be tested for by hot pressing a wet sample of the dyeing sandwiched between two pieces of dry white cotton. Color transfer to the white material indicates the presence of unfixed dye in the dyeing. It is more likely to be a problem for deep dyeing.
The use of reactive dyes is growing rapidly, faster than for any other dye application class. This is because these dyes also give dyeing of moderate to good washing fastness, allow relatively simple and diverse dyeing methods, and are available in a range of bright colors. They have contributed significantly to the decline of direct cotton dyes. Their fastness properties, though generally good, do not match those of pigmented cotton dyed with vat dyes. In particular, the fastness to bleaching by chlorine and to a lesser extent by peroxide present in modern household detergents is often only moderate.
Evidence for Covalent Bond Formation of Reactive Group with Cellulose
The good fastness to washing of dyeings with reactive dyes on cellulosic fibers is a consequence of the stable covalent bond formed between the dye's reactive group and the cellulosic polymer. There is considerable evidence to support the formation of this dye-fiber bond. Dyeing is resistant to color stripping with hot aqueous pyridine, a solvent that effectively removes direct dyes from cotton. The dyeing of cotton obtained with bifunctional dyes often exhibits reduced swelling and decreased solubility in cuprammonium solution. Adye molecule with two reactive groups crosslinking two different cellulose chains would explain this. If the color of dyeing obtained with an azo-reactive dye is destroyed by chemical reduction with alkaline sodium hydrosulfite, which cleaves the azo dye into two primary aromatic amines, the amine remaining attached to the celllulose can be diazotized and coupled with an appropriate phenol to reform a colored fiber. Finally, bacterial degradation of reactive dyes cotton that depolymerizes the cellulose, but avoids breaking the dye-fiber bond, gives colored products containing the original dye still bonded to glucose
- Anionic Detergent 1gm/L
- Non-anionic Detergent 5 gm/L
- Sequestering Agent 1 gm/L
- Hydrogen Peroxide 3 gm/L
- NaOH 3 gm/L
- Enzyme
Batch Dyeing of Cotton with Reactive Dyes
Level well-penetrated dyeings require careful preparation of the material. All sizing chemicals capable of reacting with the dye, such as starch or polyvinyl alcohol, must be removed from the material and any traces of residual alkali must be uniformly neutralized. Good alkali boiling to remove wax is essential for goods to be dyed with cold dyeing reactive dyes because the penetration of the dyes into the fibers is more difficult at lower dyeing temperatures. Reactive dyes often give such bright colors that bleaching may not be necessary. Once size has been removed, grey cotton goods can sometimes be simultaneously scoured and dyed using hot dyeing reactive dyes and an effective detergent. Because of the sensibility to bleaching by chlorine of some reactive dyes, over-chlorinated water must be avoided or treated with a reducing agent such as sodium bisulfite or thiosulphate.
Reactive Dye Process / Mechanism :
- At first anionic detergent, non-anionic detergent, sequestering agent, hydrogen peroxide, and NaOH are taken in a bath at 40 C for 10 min
- Temperature is increased slowly. Normally 2-3 C per min
- After that temperature is kept at 95-110 C for 30 minutes
- Temperature is decreased slowly
- The enzyme is added in 80 C
- After 10 min passing acetic acid is added
- After 10 minutes passing cooling and drying are completed
- Fabric is kept for 10 minutes in a bath
- Fabric is washed by overflowing process
- Finally, fabrics are prepared for dyeing
The Three-Step Exhaust Dyeing Process of Reactive Dyes
A typical exhaust dyeing process for cellulosic materials using reactive dyes has three distinct processes;
- The initial exhaustion phase: Dyeing is started in a neutral solution so that there is little likelihood of the dye reacting with the cellulose. During this stage of dyeing, some reactive dyes will be absorbed by the fibers, the amount depending upon their substantivity. This dye is capable of migration to level dyeing. Sodium chlorite or sulfite will often be present initially or be added gradually to the dye bath during this phase to promote exhaustion. The temperature of the dyebath may be gradually increased to aid penetration of the dye into the fibers and to assist migration
- The fixation phase: After the initial exhaustion phase, the PH of the dye bath is increased by the complete or gradual addition of the appropriate type and amount of alkali. This caused the dissociation of some of the hydroxyl groups in the cellulose and the nucleophilic cellulose ions began to react with the dye. The fixation process then results in additional dye absorption, to re-establish the dyeing equilibrium. Dye absorption from solution and reaction with the fiber then progress until no further dye is taken up. The variation of the dyebath exhaustion and the extent of fixation during a typical exhaust dyeing.
- The post-dyeing washing: The rinsed dyeing contains dye bonded to the cellulose, absorbed but unreacted dye, as well as hydrolyzed dye. There will also be residual alkali and salt. The latter is relatively easy to remove by successive rinsing in cold and then warm water. As much unfixed dye as possible must be washed out before dyeing. If this is not done, desorption of this dye during washing by the consumer can cause staining of other materials in the wash. Some unfixed dye is eliminated during the initial rinsing that removes alkali and salt. Through washing of the dyeing using a boiling detergent solution eliminated the remainder. The dyeing is finally rinsed in warm water. Soaping must often be repeated for deep dyeings or the residual unfixed dye must be complexed with a cationic agent.
Reactive Dyes Classification:
Reactive is very versatile and allows a variety of different approaches for controlling the rate of absorption, the rate of dye migration, and dye fixation. Salt addition, temperature variations, and alkali additions are used alone or in combination to control the dyeing process. Reactive dyes have recently been classified as:
- Akalic Controllable Dyes: which have relatively high reactivity and only moderate substantivity. They are applied at relatively low temperatures and level dyeing requires careful control of the addition of alkali to initial the fixation stage. Examples include DCT, DFCP, and VS reactive dyes.
- Salt Controlable Dyes: These are dyes of relatively low reactivity toward cotton under alkaline conditions and therefore the dyeing temperature will be as high as 80C. They have appreciable substantivity and level dyeing requires careful addition of salt to promote exhaustion. Examples in the class include TCP, MCT as well and MFT reactive dyes
- Temperature Controllable Dyes: They undergo fixation at higher temperatures even under a neutral solution.
Difference Between Vat Dye and Reactive Dye
- Reactive dye forms a covalent bond, Vat dye reacts with redox reaction and the vatting process occurs
- Reactive dyes have a good affinity to cellulosic fibers, In the vat dyeing process reducing agent hydrose provides attraction to the fibers. Again the dye is converted into insoluble form inside the fiber
- Reactive dye is easily soluble in water, and vat dye is insoluble in water
- Good affinity for water, Adding reducing agents to become soluble
- Negatively charged, removed negative charged by adding salts e.g.: NaCl. Vat dye is also negatively charged. Alkalic is used to remove negative charge
- Good substantivity for the fibers, VAT dye have good substantivity for cellulosic fibers
- The high degree of fixation efficiency, High fixation due to reducing agents
- pH range 7-11, VAT dye pH range 12- 15
- Both have good washing fastness
- Moderate rubbing fastness, poor rubbing fastness
- Reactive dye is chemically stable, chemical stability average
- Reactive dyes are applied to cellulosic, protein, and polyamide fibers i.e. cotton, and wool. Vat dyes are applied to the cellulosic and protein fibers i.e. viscose rayon, wool
- Brighter shades and dark shades available
- All colors are achievable, Major colors are indigo, green, and black
- Environment behaviour: Carcinogenic dye, Cancer causing dye
- Cost cheap, VAT dye average
- Easy process, Difficult process
- Widely used for dyeing garments i.e. Ladies wear, men wear, Kids wear, Widely used in dyeing jeans or denim
Difference Between Pigment Dye and Reactive Dye
- Reactive dye is water soluble, Pigment dye is water insoluble
- Dyes have a direct affinity to textile material, they have no affinity to textile material
- Auxochrome group are present, autochrome group are absent
- Most of the dyes are organic, Most of the dyes are inorganic
- Compatively Costly, Cheap
- No binding agent is required, the binding agent is required
- Dye diffusions in the fabric, Pigment diffusions on the fabric
What is the Difference Between Direct dyes and Reactive Dyes?
Direct dyes and reactive dyes have the potential to provide the full gamut of colors. The main difference and the advantage of reactive dyes is that they give much higher fastness than direct dyes. The reactive dye bonds covalently, double bond, with the end groups on the cotton. Providing a strong bond, which in washing running tests etc. would easily show grade 4 or 5. The direct dye would not be able to achieve these levels of performance, the addition of binders, etc. would improve the fastness but not to the reactive level and would have a detrimental effect on the handle of the fiber. Now coming back to the navy blue shade the main options would be direct dye combination, reactive dye combination, and vat dye combination. For direct dye, the total dye percent could be 2%. Considering the average cost of direct dye as Rs800/kg the cost of shade is Rs16. To get it with reactive dye it would require, say a 6 % shade. With an average dye cost of Rs300/kg, this would mean a dye cost of Rs18. The reactive dyes come in many variants MCT(Monochloro triazine) DCT( Dichloro triazine) and Vinyl sulphone(Few are suitable for discharge prints) Now the reactive dyes are available in Bifunctional groups which make the application easy at 60 degrees centigrade. Reactive Dyes are most common for cotton dyeing in the industry for their ease of application, covalent bonding, satisfactory fastness, brilliance in colors, range in colors, and economical.
Direct dyes are easy to apply but have poor wash fastness due to a weaker bond. some cheap/ economical clothes are dyed with direct dyes only. Tie-dye is one of the known applications.
Difference between hot brand and cold brand reactive dye
Cold Dyeing Brand
- Reactive cold brand dyestuffs are fiber reactive dyes which form a chemical linkage with the hydroxyl group of cellulose and thus give dyeing and printing good fastness to wet treatments
- These types of dye contain reactive groups of high reactivity. So dyeing can be done at lower temperatures i.e. 30-60 C.
- For example Procion, M Livafix
Hot Dyeing Brand
- Hot brand reactive dyes is one of the type of reactive dyes. These types of reactive dyes have lower substantivity to cotton. High dyeing temperature is required and normally dyeing at the temperature between 90-95 C. These types of dye also require a strong alkaline medium and NaOH is used to bring the pH to 10.5-11
- Hot dyes are reactive dyes for cellulosic materials and are designed to give high fixation by exhausting the dyeing method when applied at the temperature of 75-95 C
- Example: Prodion H, Cibacron
Advantages of Reactive Dyes:
- Applicable to natural and synthetic fibers
- A wide range of colors can be produced
- Can be used for dope dyeing of filament yarn
- Easily applicable
- Less expensive
- Maximum output of goods because of the elimination of washing-off, quick sampling, and high printing speed
- Good color fastness properties
- Properly produced pigment prints, using selected products
- Extremely suited for color resist effects, for example under azoic and reactive dyes
Washing-Off of Unfixed Reactive Dyes
Removal of hydrolyzed and unreactive dye from the goods is a vital step after dyeing. The amount of unfixed dye remaining in a cotton fabric dyed with reactive dyes may have to be less than 0.002%. Although bleeding out of such a small amount during subsequent washing by the consumer will not significantly alter the shade of the depth of the material, it can visibly stain adjacent white goods. This is usually unacceptable
Both batch and continuous washing processes involve three stages. Initially, the goods are rinsed in cold and warm water. This is a dilute stage aimed at removing as much salt and alkali as possible from the goods. This makes the next soaping stage much more efficient since at lower electrolyte concentrations the substantivity of the dye is less, making its desorption easier. The final stage is again a warm rinsing stage to dilute the final dye solution adhering to the fibers to the point that the amount of unfixed dye carried out to the final drying is minimal. This residual quantity of dye will deposited on the fiber surface on the evaporation of the water during drying and will be easily removed by water washing. Obviously, the amount must be as small as possible/
The entire washing operation involves achieving a compromise between the effectiveness of the removal of unfixed dye and the cost of the large volumes of water used, including the heading cost. Low liquor ratio washing saves water but gives less dilution of the washing liquors. Some dyeing machines, allow overflow rinsing but this consumes much more water. For winch and jig dyeing machines operating at atmospheric pressures, it is not possible to carry out soaping at temperatures above 90C, even when they are closed. For any given dyeing machine, each protocol is established. One point requires particular attention. After each stage in the washing cycle, dye transfers one bath to the next, in the solution retained by the fabric. This transfer must be as low as possible. This means that machines should be completely drained between stages and wash boxes in continuous washing must have effective mangles to squeeze out as much solution as possible from the fabric leaving the box
Fluorescent Reactive Dyes for Cotton Fabric:
Nowadays, Cotton
fabric dyeing with reactive
fluorescent dyes has limited color shades and brilliance. Thus, they are a group of colorants in the textile industry for dyeing cotton fabric with high demand. This research designed and synthesized two novel fluorescent reactive dyes based on fluorescein. In this respect, 4,4' -diamino stilbene-2,2- sulfonic acid and 4-aminophenyl-4-B-hydroxyl ethyl sulfone sulfate ester react with the cyanuric chloride, separately. Those that reacted with fluorescein and two reactive dyes D1 with dual-emission wavelength and D2 with an emission spectrum. The characterizations of two dyes were carried out using the TLC, HNMR, CNMR, FTIR, elemental analysis, ultraviolet spectra, and fluorimeter techniques. The absorption and emission parameters of dyes in solutions were obtained. The result indicated that the parameters of D1 were more than D2. The results show that two dyes have a positive solvatochromism effect. The synthesized dyes were applied to the cotton fabric, and their characteristics, fixation, and exhaustion percentages were studied
Dyeing Compatibility of Reactive Dyes:
Ideally, reactive dyes in a mixture should all exhaust and react with the fiber at about the same rate so that the shade builds up on tone. Dyes from different ranges,, with different reactive groups, can rarely be used together because of their different dyeing characteristics and reactivities. It is therefore usual to mix dyes with the same type of reactive group having about the same substantivity. Since there is often a great deal of uncertainty about the particular type of reactive group in a given reactive dye, dye selection must often be from one particular manufacturer's dye range and based on his recommendations
Compatible dyeing behavior is a function of all the process variables and requires careful control of the dyeing temperature, salt and alkali concentrations, dyeing time, and liquor ratios. Once the dy reacts with the cellulose, it is completely immobilized and cannot migrate. Control of the process variables determines whether a given shade will be reproducible from batch to batch. When dyeing with mixtures of reactive dyes, shading is usually possible by the addition of low substantivity dyes to the alkaline bath. The dye bath may be partially drained and refilled with cold water, the solution of shading dyes added and the bath then reheated if necessary. Further additions of salt or alkali are often not required.
Disadvantages of Reactive Dyes:
- Not controllable for the binder film
- The jamming up of equipment, and air and water pollution are observed
- Wet and rubbing fastness is average
- The handle of the printed goods is often unduly hard because of the large number of external cross-linking agents
- The original surface of the textile material is covered by the binder film. This is occasionally aesthetically effective but usually undesirable
Trade Name of Reactive Dye
Application of Reactive Dyes and Finishing Chemicals
Reactive dyes may be applied to undyed cellulosic materials at the same time as the usual crease-resist and durable press resin finishes, thus combining dyeing and finishing into one step. During curing, the methylamino groups of the polyfunctional finishing chemicals react with the hydroxyl group in the cellulose. The dye reacts with the free amino groups in this agent rather than with the fiber. Since the dye is fixed to the finishing agent, the fastness properties of the final dyeing depend on the permanence of the finish.
List of Reactive Dyes Manufacturers in India:
- Light Series Dyes Name: (Yellow R- 3R, Red R-2B, Blue R-2R, Grey RL)
- Truhromatu Shade Series: (Yellow R-4RFN, Red R-2BF, Navy blue BF, Black KN-B, G.Yellow RHB, Red RHB, Carmine RHB, Blue RHB, Navy blue RHB, Black RHB)
- Super Series : (G.Yellow RW, Orange RW, Red RW, Red RSB, Navy blue RSG, Navy blue RW, Black GN, Black RWG)
- Extreme Deep Series : (G. Yellow RHS, Red RHS, Navy blue RHS, Black RHG, Black RHR)
- Ceneral Series (Br.Yellow R-4RLN, Yellow FG, Yellow M-5R, Orange RNL, Yellow 3RS, G.Yellow R-3RD, Yellow OR, Orange KN-3G, Orange KN-GR, G.Yellow RNN, Orange T-5R, Orange KN-OU, Orange R-2RLN, Res RR, Scarlet red 2GD, Red F-2B, Red BB, Red 3BSN, Red RES, Red M-BRE, Red SNE, Red B-3BF, Red M-8B, Red R-6BF*, Deep red RD etc)
- Discharge Series : (Br. Yellow GD, Yellow GD, G.Yellow 2RD, Orange 5RD, Scarlet 2GD, Red 2BD, Carmine GD, Br, blue GD, Deep blue GD, Navy blue GD, Black RD, Black GD)
- Resist Printing Series: Br. Yellow FD, Yellow FD, Orange FD, Scarlet FD, Carmine FD, Roseo FD, Bright red FD, Violet FD, Blue FD, Br. Blue FRD, Navy blue FD, Black BD)
- Ground Color Discharge Print Series: Reactive Bright Yellow GD, Reactive Yellow GD, Reactive Golden Yellow GD, Reactive Orange 5RD, Reactive Scarlet 2GD, Reactive Rosy Red 2BD, Reactive Red BD, Reactive Brilliant blue GD, Reactive Deep blue GWD, Reactive Navy blue BD, Reactive Black RD, Reactive Black GD)
- Wool Reactive Dyes: ( Wool Reactive Bright Yellow WG, Wool Reactive Golden Yellow WR, Wool Reactive Orange WR, Wool Reactive Scarlet WG, Wool Reactive Brilliant Red WB, Wool Reactive Bordeaux W2G, Wool Reactive turquoise blue WG, Wool Reactive Brilliant blue WB, Wool Reactive Brilliant blue WR, Wool Reactive Navy blue WG, Wool Reactive Navy blue WR, Wool Reactive Black WR, Wool Reactive Black WG)
F.A.Q
What is an example of a reactive dye?
Procion Yellow MR is an example of cold brand reactive dye.
Why reactive dye is so called?
Reasons for so called because this is the only type of dye, which has reactive group, that reactive group chemically reacts with fiber polymer molecules and form covalent bonds. For this reason they are so called. They are also called fiber reactive group
Reason Why use reactive dyes?
Because these dyes are more chemically reactive than any other fibers, they can react with different type of fabrics, resulting in stronger chemical bonds that make the dye more durable
What is the principle of reactive dyes?
The dyeing principle is based on fiber reactivity & involves the reaction of a functional group of dyestuff with a site on fiber to form a covalent link between dye molecule & substance. 4 structural features of typical reactive dye molecules are:
1.
Chromophoric grouping, contributing color
2. Reactive system, enabling dye to react with hydroxy group in cellulose. 3. A bridging group that links the reactive system to the chromophore,
4. One or more solubilizing group, usually sulphuric acid substituents attached to the chromophore group for their color, although Azo chromophore- N-N- is by itself the most important.
All reactive dyes contain sodium sulphonate group for solubility & dissolve in water to give colored sulphonate anions & sodium cations. Most reactive dyes have 1 to 4 of these sulphonate groups: The general form of reactive dye is as follows:
S -R-------B-------X
S- Water solubility group
RChromophore
X Reactive System
B-Bond between reactive system & Chromophore
The dyeing principle is based on fiber reactivity & involves the reaction of a functional group of dyestuff with a site on fiber to form a covalent link between dye molecule & substance. 4 structural features of typical reactive dye molecules are 1.
Chromophoric grouping, contributing color
2. Reactive system, enabling dye to react with hydroxy group in cellulose. 3. A bridging group that links the reactive system to the chromophore,
4. One or more solubilizing groups, usually sulphuric acid substituents attached to the chromophore group for their color, although Azo chromophore- N-N- is by itself the most important.
All reactive dyes contain sodium sulphonate group for solubility & dissolve in water to give colored sulphonate anions & sodium cations. Most reactive dyes have 1 to 4 of these sulphonate groups: The general form of reactive dye is as follows:
S -R-------B-------X
S- Water solubility group
RChromophore
X Reactive System
B-Bond between reactive system & Chromophore
Comments
Post a Comment