Dyeing Faults Causes and Remedies
Major dyeing faults in dyeing process is mentioned as follows.
- Uneven Dyeing
- Batch to Batch Shade Variation
- Patchy Dyeing Effect
- Roll to Roll Variation or Meter to Meter Variation
- Crease Mark
- Dye Spot
- Wrinkle Mark
- Softener Mark
Uneven Dyeing:
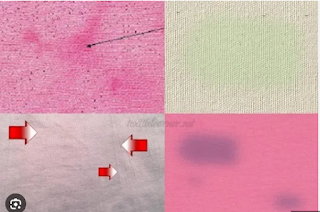 |
Fig: Uneven Dyeing |
Causes:
- When uneven pretreatment occurs (i.e. uneven scouring and bleaching)
- Improper color dosing in the dye tank
- When high fixation dyes uses
- In case of synthetic fibers, uneven heat setting
- Lack of maintenance of dyeing machine
Remedies:
- Ensure even pretreatment
- Ensure even heat-setting in the case of synthetic fibers
- Proper dosing of dyes and chemicals
- Proper controlling of dyeing machine.
Batch to Batch Shade Variation
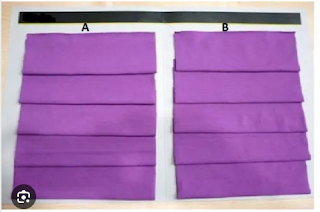 |
Fig: Batch to Batch Shade Variation |
Causes
- Temperature fluctuation
- Dyes and chemicals improper dosing time
- Dyes and chemicals batch-to-batch weight variation
- Variation of dyes lot
- Improper liquor ratio, reel speed, pump speed
- Improper pretreatment
Remedies:
- By using standard dyes and chemicals
- The same liquor ratio needs to be maintained
- By following standard pretreatment procedure
- The same dyeing cycle needs to maintain
- An identical dyeing procedure should be followed
- The operators need to add the right bulk chemicals at the same time and temperature in the process
- The pH, hardness, and sodium carbonate content of supply water should check daily
Patchy Dyeing Effect
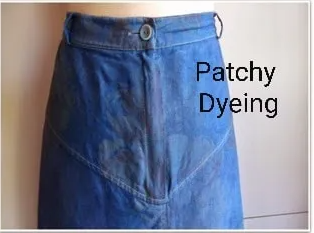 |
Fig: Patchy Dyeing Effect |
Causes
- Fabric entanglement
- Alkali faulty injection
- Color improper addition
- Due to water hardness
- Due to the addition of improper salt
- During intermediate dyeing, dye migration
- Uneven heat in the machine etc.
Remedies:
- Proper pretreatment needs to be ensure
- Dyes and chemicals proper dosing
- Heat should be the same throughout the dye liquor
- Proper addition of salt
Roll to Roll Variation or Meter to Meter Variation
Causes
- Dyes poor migration property
- Improper solubility of dyes
- Water hardness
- Faulty machine speed, etc.
Remedies
- Use of standard dyes and chemicals
- Proper machine speed need to maintain
- Use of soft water
Dye Spot
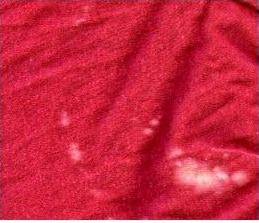 |
Fig: Dye Spot |
Causes
- Dye particles improper dissolving in batch
- Caustic soda particle improper dissolving in bath
Remedies
- Dyes and chemicals need to be properly dissolve
- Bypassing the dissolved dyestuff through a fine stainless steel mesh strainer
Crease Mark
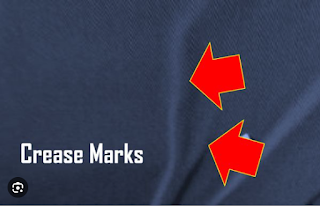 |
Fig: Crease Mark |
Causes
- The fabric rope poor opening
- Synthetic material shock cooling
- If pump pressure & reel speed in not equal
- Due to high speed machine running
Remedies
- Proper reel speed and pump speed maintaining
- Lower rate rising and cooling temperature
- Reducing machine load
- Higher liquor ratio
Wrinkle Mark
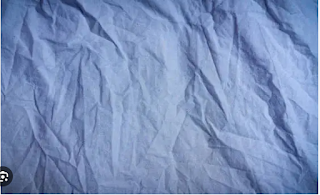 |
Fig: Wrinkle Mark |
Causes
- The fabric rope poor opening
- Shock cooling synthetic material
- High temperature entanglement of the fabric
Remedies
- Maintaining of proper reel and pump speed
- Cooling the temperature and lower rate rising
- Liquor ratio need to be remain higher
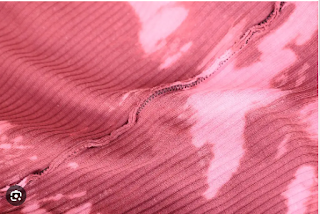 |
Fig: Softener Mark |
Causes
- Softerner improper mixing
- During application of softener, improper fabric running time
- Fabric entanglement during application of softener
Remedies
- Proper reel speed and pump speed should be maintained
- Proper mixing of softener before the addition of the softener
- During softener application, prevent the entanglement of the fabric
Comments
Post a Comment