Textile Manufacturing Process
Textiles have been an integral part of human civilization for centuries, serving both practical and aesthetic purposes. From clothing and household items to industrial applications, textiles play a vital role in our everyday lives. In Textile Engineering textile manufacturing process is the heart of textile to be able to an affluent textile engineer. Behind the fabric that drapes us, covers our furniture, and adorns our surroundings lies a fascinating and intricate manufacturing process. In this blog, we'll take you on a journey through the various stages of textile manufacturing, shedding light on the remarkable journey from raw fibers to finished textiles.
- Fiber Selection and Preparation
The journey of textile manufacturing begins with the selection of appropriate raw materials, known as fibers. These fibers can be natural, such as cotton, silk, wool, or linen, or synthetic, including polyester, nylon, and acrylic. The chosen fiber greatly influences the texture, appearance, and properties of the final textile.
Once selected, the fibers undergo cleaning, sorting, and blending processes to remove impurities and create a consistent material. This preparation ensures that the fibers are ready for the subsequent stages of production. Without the selection of proper fiber, Textile manufacturing cannot be done properly.
- Spinning
Spinning is the second fundamental process of textile manufacturing. It is the process of transforming raw fibers into yarn, the fundamental building block of textiles. This stage involves twisting and stretching the fibers to create a continuous strand of thread. Traditional methods involve using a spindle, while modern manufacturing employs spinning machines for increased efficiency and precision. The thickness and quality of the yarn determine the textile's strength, durability, and texture.
- Weaving or Knitting
In the Textile manufacturing process, there are three processes to form fabric such as weaving, knitting, and non-woven process. After spinning, the yarn is ready to be transformed into fabric through weaving or knitting. In weaving, vertical (warp) and horizontal (weft) threads intersect at right angles to create various patterns. Different weaving techniques, such as plain, twill, and satin weaves, produce different textures and appearances.
 |
Weaving Process |
Knitting, on the other hand, involves interlocking loops of yarn to create fabric. This technique offers greater flexibility and is commonly used for knitwear and stretchy materials.
- Dyeing and Printing
Dyeing is the most important part of the textile manufacturing process. Once the fabric is woven or knitted, it's often treated with dyes or prints to enhance its aesthetic appeal. Dyeing involves immersing the fabric in a colored solution, allowing the fibers to absorb the dye. Printing uses various methods, such as screen printing, digital printing, and block printing, to apply patterns or designs onto the fabric's surface.
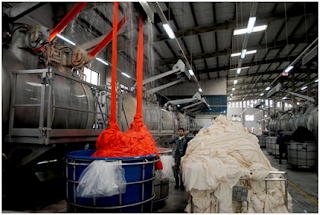 |
Dyeing Process
|
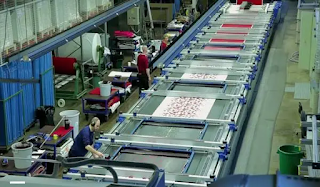 |
Printing Process |
- Finishing
Finishing is a crucial step that enhances the textile's appearance, texture, and functionality. It involves processes like bleaching, sizing, and coating to improve qualities such as softness, water resistance, and wrinkle resistance. Finishing can also include mechanical processes like brushing or sanding to achieve specific textures.
Finishing Process
- Quality Control
Throughout the manufacturing process, rigorous quality control checks are performed to ensure that the textiles meet the desired standards of process control in textile manufacturing. These checks encompass various factors, including color consistency, fabric strength, dimensional stability, and overall appearance. We get deep knowledge about this process control in textile manufacturing pdf
Flow Chart Of Textile Manufacturing Process:
The textile manufacturing process is the process flow of making a finished desired garments.
At first, fiber is collected from the plant by applying different methods such as harvesting, cotton pickers, strippers, and cotton ginning process.
Then, fiber is transferred to the spinning mills where fibers are turned into yarn through various processes such as bale management, blow room, carding, drawing, combing, roving process, etc.
Yarn can be turned into fabric by mainly two processes such as weaving, knitting, etc. In weaving, yarn can be used as warp and weft yarns where they interlaced with each other. In knitting, yarns are used as wales and course yarn where they interloop or intermesh with each other. Non-woven fabric also exists as a fabric but it is mainly made from fiber.
Then, Grey fabric is delivered to the dyeing mill to get the desired color of the fabric. In dyeing, different processes are used to dye different types of fabric. For instance, cotton fabric is dyed by using reactive dye, and jeans and denim fabrics are dyed with vat or sulfur dye. Polyester fabrics are dyed by using dispersed dye. Different mordants, enzymes, and natural dyes are used to dye fabric. These fabrics are dyed by using various processes such as continuous, semi-continuous, cold pad batch, and thermos dyeing processes, etc. Different types of machines are used to dye fabric such as jet, jigger, winch dyeing, etc.
After getting the desired color fabric, the fabric is delivered to the garments for sewing. In sewing various processes are used to make finished garments. To make the garments as per buyer requirements, they need to go through the following processes such as design/sketch, basic block, working pattern, sample making, marker making, production pattern making, fabric spreading, cutting, sorting, bundling, sewing, garments inspection, ironing, final inspection, packing, cartooning and delivery, etc in textile engineering.
Flow Chart of Cotton Fiber Manufacturing:
- Fiber Harvesting
- Fiber Strippers
- Fiber Pickers
- Cotton Ginning
Flow Chart of Spinning (Carded Yarn) :
- Bale Management
- Blow Room
- Carding Machine
- 1st Draw Frame
- 2nd Draw Frame
- Simplex/Speed Frame/Roving Frame
- Ring Frame
Flow Chart of Spinning (Combed Yarn) :
- Bale Management
- Blow Room
- Carding Machine
- Pre-Comb Drawing
- Lab Former
- Combing
- Post Comb Drawing
- Simplex/Speedframe/Roving Frame
- Ring Frame
Flow Chart of Weaving:
- Cone Winding ( Weft Yarn Pirn or Cone)
- Warping(Sectional Warping and Beam Warping)
- Sizing
- Draw-in
- Tie-in or Knotting
- Weaving
- Grey Fabric Inspection
Flow Chart of Knitting:
- Yarn in Cone Package Form
- Place the Yarn Package in the Reel
- Feeding the Yarn in the Feeder
- Set the Machine as the design and GSM
- Knitting
- Withdraw the Roll Fabric and Weighing
- Roll Making
- Inspection
- Numbering
- Dispatch
Flow Chart Of Dyeing Process:
- Grey Fabric Inspection
- Batch Section
- Stitching
- Load on Machine
- Scouring
- Bleaching
- Enzyme
- Leveling
- Electroplating
- Dyeing
- Softening
- Unload Fabric from the Machine
Flow Chart of Garments Manufacturing Process:
- Design or Garments Sketch
- Basic Block
- Working Pattern
- Sample Making
- Production Pattern
- Marker Making
- Fabric Spreading
- Cutting
- Sorting
- Bundling
- Sewing
- Garments Inspection
- Ironing and Finishing
- Final Inspection
- Packing
- Cartooning
- Delivery
Technical Textile Fabric Manufacturers List in Bangladesh:
- Fakir Group
- Akij Textiles Limited
- Hameem Group
- Beximco Apparels Ltd
- Square Fashions Ltd
- DBL Group
- Epyllion Group
- Masco Industries Ltd.
- Asian Apparels Limited
- Posh Garments Ltd
Top 10 Textile Machinery Manufacturers in the World:
Below machines are the textile manufacturing machinery companies in the world. Textile Machinery Manufacturers in India, Textile Machinery Manufacturers in Coimbatore, Textile Machinery Manufacturers in Suart, and Textile Machinery Manufacturers in Ahmedabad people will also want to know about this machine to get better knowledge in textile engineering.
- Zimmer- Screen Printing Machines, Digital Printing Machines, Coating Machines: Austria
- Trutzchler- Spinning Machines, Man-made fiber machines, woven fabric machines: Germany
- Oerlikon- Manmade fiber spinning system texturing machines- Switzerland
- Rieter- Systems, products, components, and digitization solutions for short-staple fiber spinning: Switzerland
- Saurer- Pre-spinning machines, spinning machines, Twisting & cabling machines, winding machines, and Embroidery machines: Switzerland
- Biancalani- Textile Finishing Machines: Italy
- Dilo Group- Non-Woven Machines- Germany
- Bruckner - Textile Machinery: Germany
- Stoll- Flat Knitting Machine: Germany
- Karl Mayer- Warp Knitting Machine, Warp Preparation Machine: Germany
- Shima Seiki- Knitting Machine Design System: Japan
- Mayer & Cie- Circular Knitting Machine: Germany
- Groz Backert- Knotting Machine: Germany
- Ruti - Projectile Weaving Machine: Switzerland
- Tupesa - Dyeing Machine: Spain
- Juki- Sewing machine: Japan
- Jack- Sewing Machine: China
- Textile Sizing Chemical Manufacturers: China
Textile Manufacture:
Textile consumption is closely related to the growing world population and consumer affluence. To satisfy market demand for fabric, fully automated, high-speed production with minimum defects is essential. The following outline of textile manufacturers identifies the major processes, the division of operations, and the division of operations, and situates coloration in the overall scheme.
Cotton and wools are only available as short stable fibers of predetermined length, but artificially made fibers are available as continuous filaments or short fibers to cut any required length. Textile manufacturers using natural fibers start with the opening, separation, and mixing of short fibers. The carding process draws them into a band of parallel fibers, drawing out and twisting that yield spun yarn. Opening, carding, or drawing may also serve to blend two or more stable fibers for example cotton and staple polyester. Continuous filaments do not require such preliminary operations
The major methods of fabric assembly from yarns of stable fibers or from continuous filaments are weaving and knitting. Both of which are fully automated, and have significant production rates.
The production of textile material from fibers involves a defined sequence of operations to produce yarns and assemble them into the fabric. Each process is a necessary prerequisite for the next process. The situation of dyeing in the production scheme, however, is not necessarily defined. Dyeing may occur at any stage during textile manufacture: on loose fiber, or on the intermediate forms such as sliver, yarn, or fabric towards the end of the manufacturing cycle. Even garments and finished articles can be dyed. This means that a variety of dyeing machines is required for the different types of textiles. Dyeing usually involves contact between an aqueous solution or dispersion of the dyes and the textile material, under the condition that promotes substantivity and produces uniform coloration throughout. Printing, on the other hand, localized the application of different dyes to different specific areas on one face of fabric, according to some predetermined color design.
Before textile fibers are dyed, they are washed or scoured to remove natural impurities, lubricating oils, and size. Bleaching eliminates any colored impurities and is often necessary for white goods containing natural fibers, and before dyeing pale, bright shades. This stage of production is called preparation. Its objective is to clean the material before dyeing and finishing so that it wets easily and uniformly absorbs the solution of chemicals and dyes. Poor quality preparation, particularly when it is uneven, is a major cause of faulty dyeings.
The final stage in the manufacture of textiles is finishing. This involves treatments to improve the appearance or performance of the material. It might consist of a single mechanical process such as calendering ( to give the fiber a flat or compact surface) or napping ( to break fibers or raise the ends forming a pile). Modification of the functional characteristics of the fabric often involves a chemical finishing. The process ranges from the simple application of a softening agent to improving the material's handling and reducing static electricity. Most chemical finishing is for fabrics of natural fibers, particularly for those containing cotton. This satisfies consumer demand for cotton materials having the easy-care characteristics associated with fabrics made from synthetic fibers. Many finishing chemicals, particularly those involving chemicals, can modify both the color and the fastness properties of a dyed fabric, and these effects must therefore be known in advance. Piece dyeing usually refers to the dyeing of fabric as distinct from the dyeing of a completed article such as a garment. Textile manufacture is highly specialized.
Type of Process Specific Process Industrial Unit
Yarn Production 1. Opening Spinning Mill
2. Carding
3. Spinning
Fabric Construction 4. Knitting Knitting Mill
Preparation 5. Scouring
6. Bleaching
Coloration 7. Dyeing Dyehouse or finishing mill
Finishing 8. Mechanical or
Chemical finishing
Consequently, yarn production, fabric construction, and dyeing and finishing often take place in different locations with a clear division between the mechanical manufacturing operations and the wet processing associated with preparation, dyeing, or printing and finishing.
The seven major fiber types have quite different properties. The materials produced from these have a wide variety of end-uses, each fabric has its particular aesthetic, color fastness, and technical requirements. There are therefore different types of dyes and processing methods for dyeing and printing. The manufacture of any fabric will always involve a compromise between the desired quality and performance, and the overall production cost. Today, fully automated, and environmentally friendly processes are the norm: automation is essential to remain competitive, and national and local governments now demand lower levels of air and water pollution. The environmental impact of textile production and coloration is the most significant challenge facing the industry in Europe and North America today. Eventually, more environmentally sound methods of production and disposal will also be forced upon producers in the developing world as they expand further.
Fiber Identification Burning Test:
.
Cotton:
When ignited it burns with a steady flame and smells like burning leaves. The ash left is easily crumbled. Small samples of burning cotton can be blown out as you would a candle.
.
Linen
Linen takes longer to ignite. The fabric closest to the ash is very brittle. Linen is easily extinguished by blowing on it as you would a candle.
.
Silk
It is a protein fiber and usually burns readily, not necessarily with a steady flame, and smells like burning hair. The ash is easily crumbled. Silk samples are not as easily extinguished as cotton or linen.
.
Wool
It is also a protein fiber but is harder to ignite than silk as the individual "hair" fibers are shorter than silk and the weave of the fabrics is generally looser than with silk. The flame is steady but more difficult to keep burning. The smell of burning wool is like burning hair.
.
Man Made Fibres
.
Acetate
Acetate burns readily with a flickering flame that cannot be easily extinguished. The burning cellulose drips and leaves a hard ash. The smell is similar to burning wood chips.
.
Acrylic
Acrylics burn readily due to the fiber content and the lofty, air-filled pockets. A match dropped on an acrylic blanket can ignite the fabric which will burn rapidly unless extinguished. The ash is hard. The smell is acrid or harsh.
.
Nylon
Nylon melts and then burns rapidly if the flame remains on the melted fiber. If you can keep the flame on the melting nylon, it smells like burning plastic.
.
Polyester
Polyester melts and burns at the same time, the melting, burning ash can bond quickly to any surface it drips on including skin. The smoke from polyester is black with a sweetish smell. The extinguished ash is hard.
.
Rayon
It is a regenerated cellulose fibre which is almost pure cellulose. Rayon burns rapidly and leaves only a slight ash. The burning smell is close to burning leaves.
.
Limitation of Burning Test:
Many fibers have similar burning reactions that might cause doubt and occasional confusion.
Conclusion:
The journey from raw fibers to finished textiles is a remarkable fusion of art, science, and technology in textile engineering. The intricate processes involved in textile manufacturing highlight the ingenuity of humanity in creating materials that cater to both our functional and creative needs. As you don your favorite garments or relax on your cozy couch, take a moment to appreciate the craftsmanship and innovation that go into every thread of fabric that surrounds you. Chorka Textile and Square Textile are the leading factories in textile manufacturing processes. From the Google Maps location, we get the idea about textile manufacturing companies near me. To Know about process control in textile manufacturing pdf click here
Comments
Post a Comment